Supply chain digitalisering in de praktijk
Van aardappel tot vork
In de afgelopen zeven jaar hebben we de volledige supply chain van aardappel tot friet gedigitaliseerd. Wat ooit afhankelijk was van talloze Excel-lijsten en handmatige communicatie, is nu een volledig geïntegreerd proces. Dankzij deze digitale transformatie verlopen de stappen in de keten soepeler, sneller en efficiënter.
De reis van de aardappel begint bij de leverancier, gevolgd door transport naar de fabriek. Na verwerking in de fabriek gaat de friet via gekoeld transport naar de vrieshuizen. Vanaf daar wordt de friet verder vervoerd, zowel over land als over zee, naar de eindbestemmingen zoals restaurants en retailers wereldwijd. In dit artikel belichten we hoe wij de processen in elke stap van deze keten heeft geoptimaliseerd.
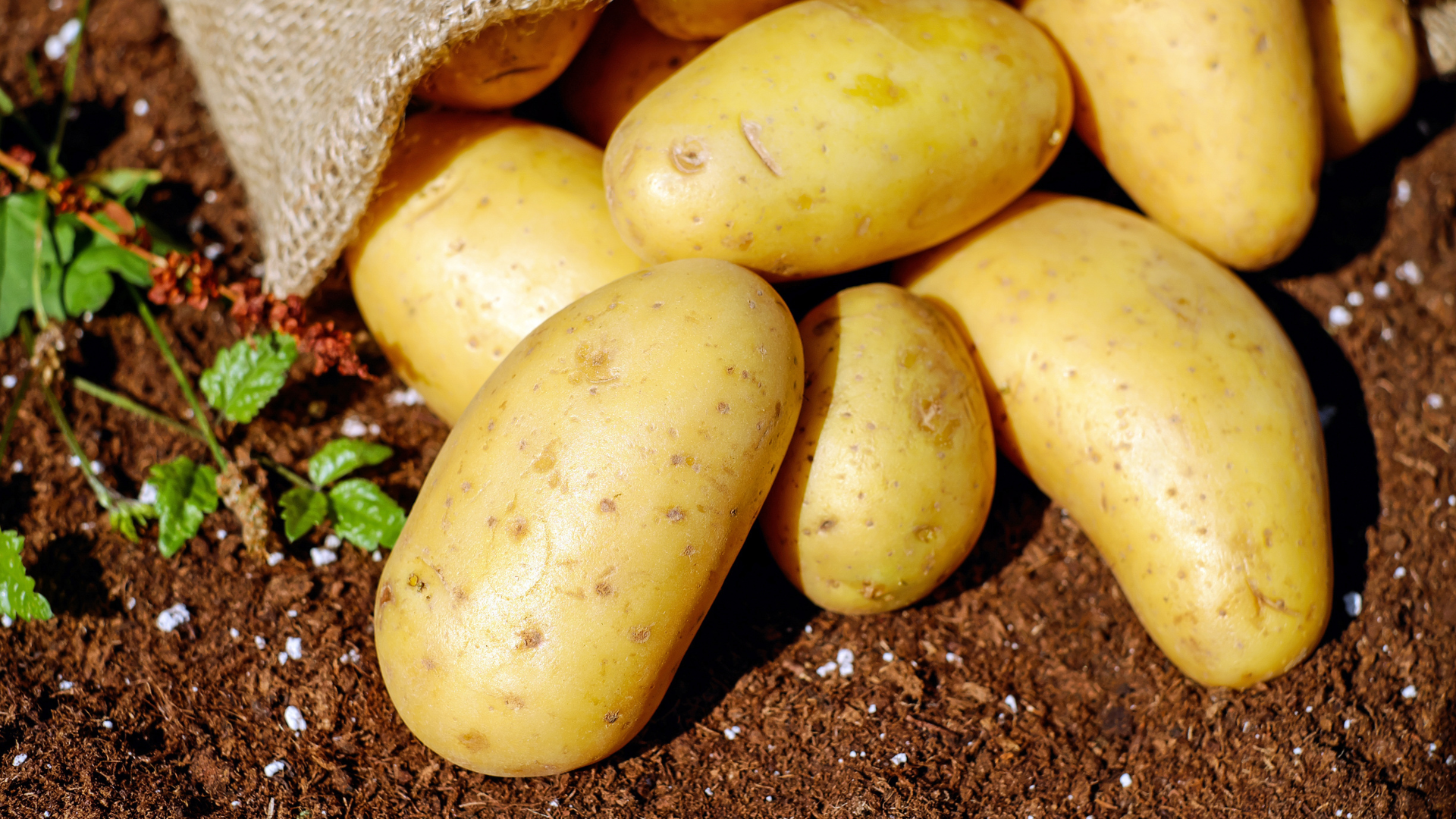
Optimalisatie als sleutel tot succes
Digitalisering supply chain
Bij het digitaliseren van de supply chain draait alles om het optimaliseren van bedrijfsprocessen. In het project van aardappel tot friet hebben we elke schakel – van de toeleveringsketen tot distributie – opnieuw ingericht. Met maatwerksoftware en innovatieve tools hebben we unieke uitdagingen aangepakt en de efficiëntie verhoogd.
Dankzij deze digitale transformatie is de hele keten niet alleen efficiënter, maar ook flexibeler geworden. We laten zien hoe wij in elke fase waarde hebben toegevoegd.
Waar digitalisatie begint
Manufacturing: proces in de fabriek
De digitalisatie begint zodra de aardappel de fabriek binnenkomt en wordt verwerkt tot friet. Dit proces is geoptimaliseerd met specifieke applicaties:
Voorraadsysteem
Automatiseert het voorraadbeheer van essentiële grondstoffen zoals olie. Zodra het oliepeil onder een bepaald niveau komt, stuurt het systeem automatisch een melding naar de transporteur om levering te plannen. Dit voorkomt productiestilstand.
Klachtenregistratiesysteem
Een ketenbrede tool waarmee alle partijen – van leveranciers tot verkooppunten – eventuele klachten kunnen registreren en opvolgen.
De data in deze systemen wordt verzameld uit recepten, productieplanningen en realtime tankstanden. Door integraties en nauwkeurige planning wordt het productieproces efficiënt aangestuurd, met minimale risico’s op onderbrekingen.
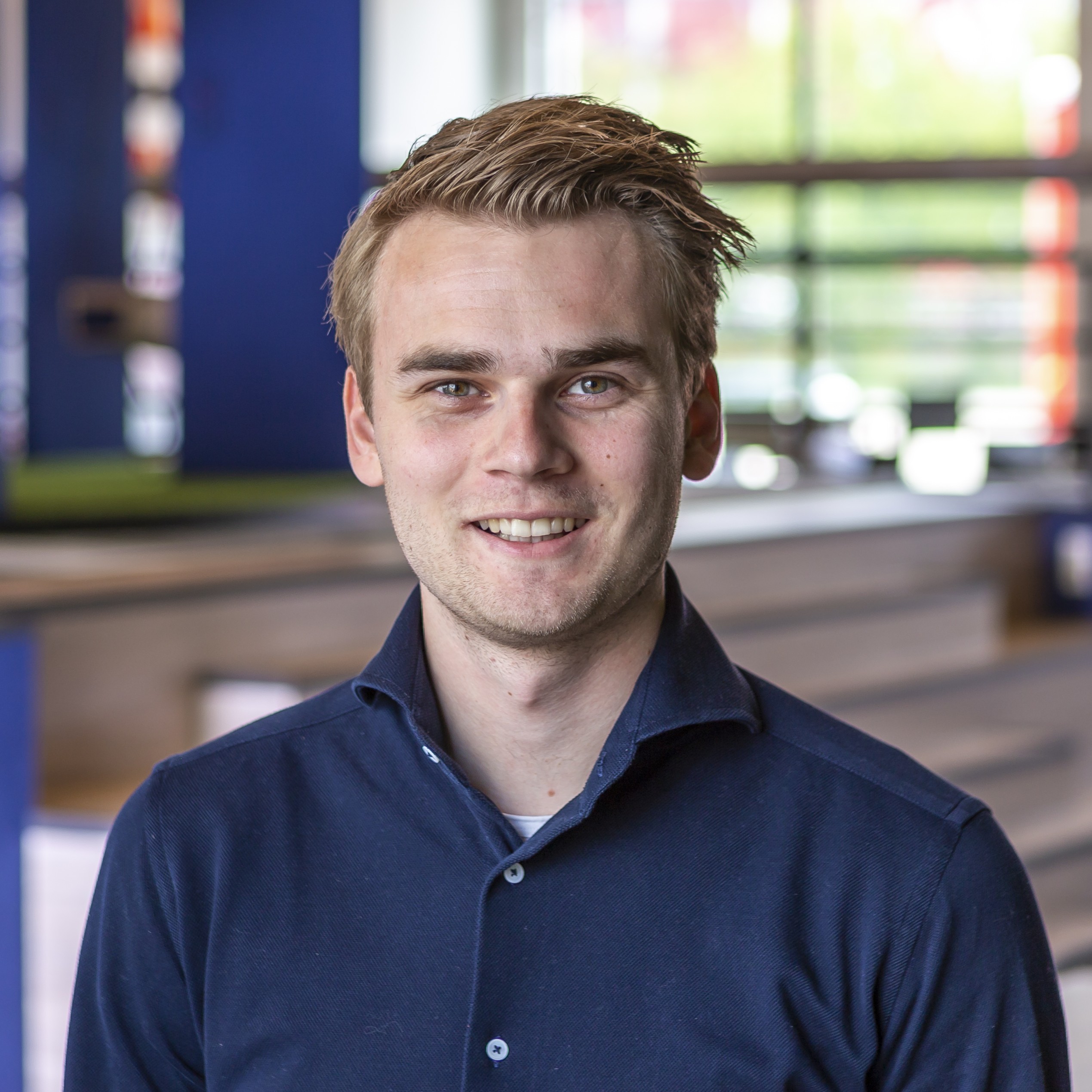
Youri aan het woord
De data die in de applicatie wordt bijgehouden komt uit drie bronnen:
- Recepten (verbruik per uur, per KG). Dit wordt handmatig ingelezen in de applicatie. Hoeveel olie is er nodig om een bepaald product te bakken.
- Productieplanning met een start en eindtijd. Dit wordt ook handmatig ingelezen.
- Via een integratie worden de actuele tankstanden automatisch per uur ingelade
Er zijn verschillende productielijnen met verschillende types olie. Door de productieplanning in te laden in combinatie met de data die aanwezig is in de applicatie worden constant verwachte tankstanden berekend en kan de leverancier inzien wanneer er een levering gedaan moet worden.
Grip op gekoeld transport
Transport B: van fabriek naar vrieshuis
Na verwerking in de fabriek wordt de voorgebakken friet ingevroren en vervoerd naar verschillende vrieshuizen. Tijd en temperatuur zijn in deze fase cruciale factoren. CAPE heeft verschillende applicaties ontwikkeld om dit proces te ondersteunen:
Klantportaal
Hier kunnen producenten hun transportorders plaatsen, beheren en volgen via track-and-trace-functionaliteit. Dankzij een Power BI-dashboard hebben gebruikers realtime inzicht in hun orders.
AI-aangedreven PDF-omzetting
Bestelgegevens worden automatisch verwerkt, Ongeacht de samenstelling van de PDF, weet het systeem nu binnen enkele seconden de PDF om te zetten in een voor systemen begrijpbare JSON-tabel. Dit scheelt de transporteur vele uren handmatig overtypen van verstuurde orderverzoeken en zorgt voor consistente data-uitwisseling.
Emballagebeheer
Een applicatie voor het volgen van pallets en ladingdragers, ontwikkeld op basis van ons Emballage Management Systeem. Dit houdt statiegeldbalansen helder en beheersbaar.
Efficiënte doorlooptijd en dockplanning
Warehouse: vrieshuizen
In de vrieshuizen wordt de friet opgeslagen voor verdere distributie. De uitdaging is om de doorlooptijd te minimaliseren en tegelijkertijd de temperatuur van de producten te garanderen. Hiervoor ontwikkelden we de dockplanning:
Dockplanning
De planning is zowel voor het beheren van de inbound orders, als outbound orders. Dit dockplanningssysteem geeft transporteurs de mogelijkheid om zelf een tijdslot te boeken voor laden en lossen. Hierdoor weten de vrieshuis medewerkers precies, hoe laat welke order, bij welk dock klaar moet staan of aankomt en is het laden/lossen vele maler efficiënter ingericht. Dit voorkomt wachttijden bij de docks.
WMS-integratie
De dockplanning stuurt geplande ritten door naar het Warehouse Management System (WMS) en ontvangt statusupdates over laad- en vertrektijden. Deze data zijn weer beschikbaar voor monitoring en rapportage.
Wereldwijde distributie op maat
Transport C: over land en zee
Vanuit de vrieshuizen gaat de friet verder naar retail- en horecalocaties, zowel binnen Europa als daarbuiten. Deze fase brengt unieke uitdagingen met zich mee, zoals het inplannen van charters en het voldoen aan internationale standaarden.
In principe gaat het vervoer via wegtransport met een vaste transporteur. Echter komt het dusdanig vaak voor dat extra vrachtwagens en chauffeurs extern worden ingehuurd, dat in dit deel van de keten een charterportaal op maat is ontwikkeld voor de frietreis. Charters geven tijdens hun rit in het portaal aan wanneer zij vertrekken en wanneer zij op bestemming zijn. Op deze manier is er ook weer continue inzage in waar de friet zich bevindt.
Om met deze uitdagingen om te gaan bieden wij in deze fase van de supply chain oplossingen als:
Cloudscraper
Automatiseert ETA-updates door scheepsinformatie van rederijwebsites te scrapen. Dit is vooral nuttig voor rederijen die nog niet voldoen aan de DCSA-standaard.
Charterportaal
Een charterportaal waarmee ingehuurde chauffeurs hun ritten realtime kunnen registreren. Dit geeft continu inzicht in de status van transporten.
Control Tower
Deze applicatie houdt het volledige proces van order tot levering in de gaten. Voor zeevracht werken we met de DCSA-standaard; voor wegtransport met het Open Trip Model.
Stap 1: Ontvangst van orders
- De hoofdtransporteur plaatst alle frietorders in de Control Tower.
- Orders bevatten details zoals hoeveelheid, containervereisten en bestemming.
Stap 1: Ontvangst van orders
- De hoofdtransporteur plaatst alle frietorders in de Control Tower.
- Orders bevatten details zoals hoeveelheid, containervereisten en bestemming.
Stap 2: Inplannen van schepen en containers
- De orders worden gekoppeld aan specifieke schepen en containers.
- Het systeem voegt automatisch de juiste containergewichten en douanedocumenten toe aan de planning.
Stap 3: Standaardisatie van berichtgeving
- Het gehele orderproces wordt gestroomlijnd volgens de DCSA-standaard.
- Feedback van onze consultants heeft geleid tot verdere verfijning van de standaard, wat bijdraagt aan betere gegevensuitwisseling en consistentie.
Stap 3: Standaardisatie van berichtgeving
- Het gehele orderproces wordt gestroomlijnd volgens de DCSA-standaard.
- Feedback van onze consultants heeft geleid tot verdere verfijning van de standaard, wat bijdraagt aan betere gegevensuitwisseling en consistentie.
Stap 4: Automatische ETA-generatie
- Na het inplannen van een order genereert het systeem een geschatte aankomsttijd (ETA).
- Deze ETA wordt direct zichtbaar in het klantportaal, zodat opdrachtgevers weten wanneer ze hun order kunnen verwachten.
Stap 5: Realtime monitoring van transport
- Eventuele vertragingen worden automatisch gedetecteerd en gecommuniceerd via het klantportaal.
- De transportstatus is altijd actueel, inclusief wijzigingen in aankomsttijden.
Stap 6: Inzicht in de volledige vaart
- De Control Tower biedt een visueel overzicht van de gehele route.
- Zowel de transporteur als de retaillocaties kunnen zien waar de friet zich bevindt en welke stappen al zijn doorlopen.
Integratie als gamechanger voor supply chain management
Vrijwel alle bovenstaande applicaties en de rest van de IT-landschappen, van zowel de producent en de vervoerders over land en over zee, zijn met elkaar geïntegreerd via ons integratieplatform eMagiz. Dit betekent dat via één platform alle berichtstromen lopen en zowel interne als externe applicaties met elkaar data uit wisselen.
Omdat gebruik wordt gemaakt van het Open Trip Model en de DCSA standaard, zijn voor beide aparte validatie componenten gemaakt.
Is een bericht bestemd voor de zeevracht? Dan zal het bericht eerst worden gevalideerd volgens de DCSA standaard, alvorens het bericht verder de keten in gaat. Hetzelfde geldt voor berichten voor de orders die over land worden vervoerd. Deze berichten gaan eerst via de Open Trip Model validatie connector.
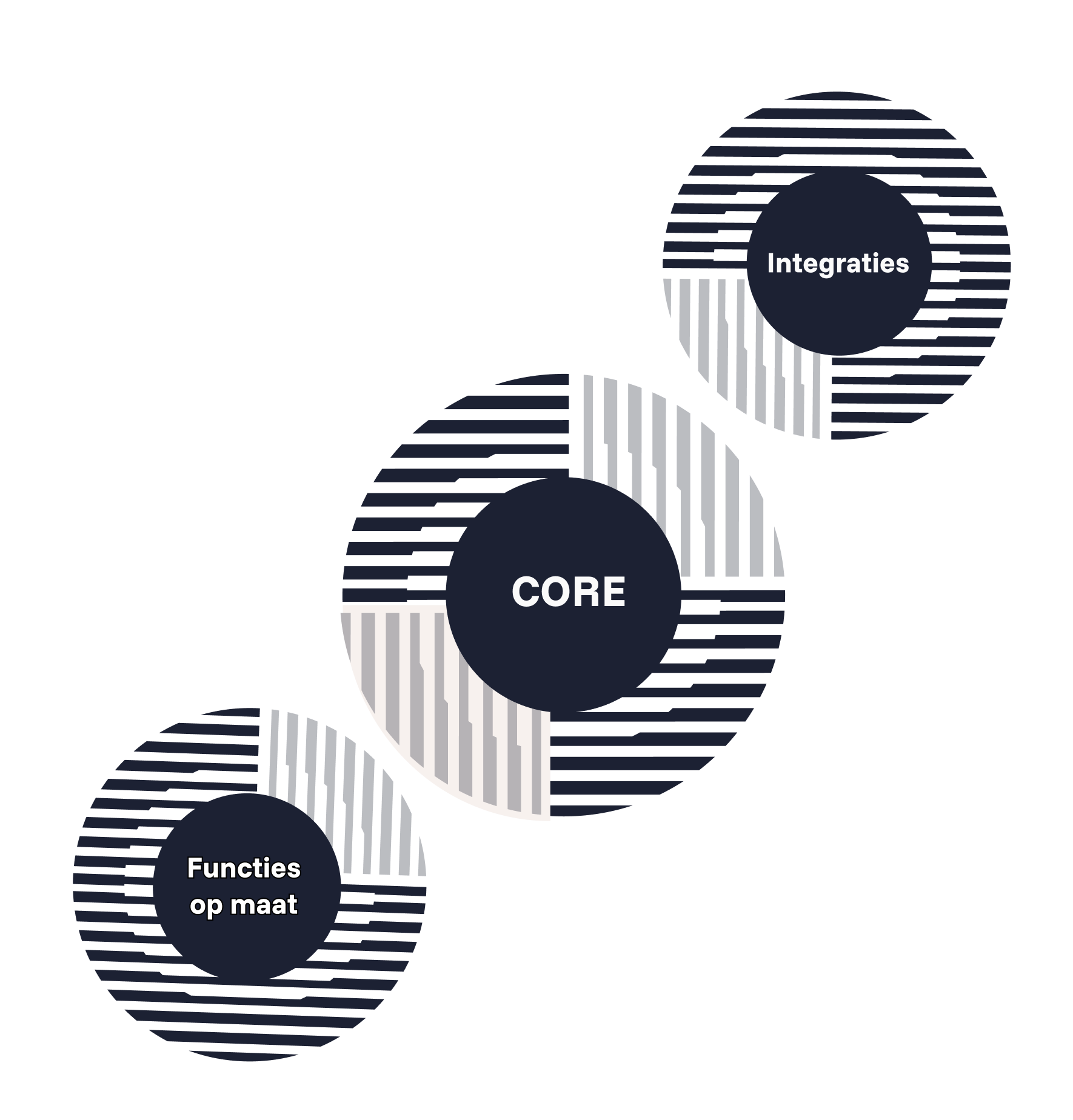
Het resultaat
De digitalisatie van deze supply chain heeft gezorgd voor:
- Realtime inzicht: Naadloze data-uitwisseling via eMagiz, ons integratieplatform.
- Efficiëntie: Kortere doorlooptijden en minder handmatige processen.
- Schaalbaarheid: Oplossingen die meegroeien met de behoeften van de klant.
Door standaarden zoals DCSA en het Open Trip Model te combineren met onze expertise in integratie, hebben we een flexibele en toekomstbestendige keten gecreëerd.